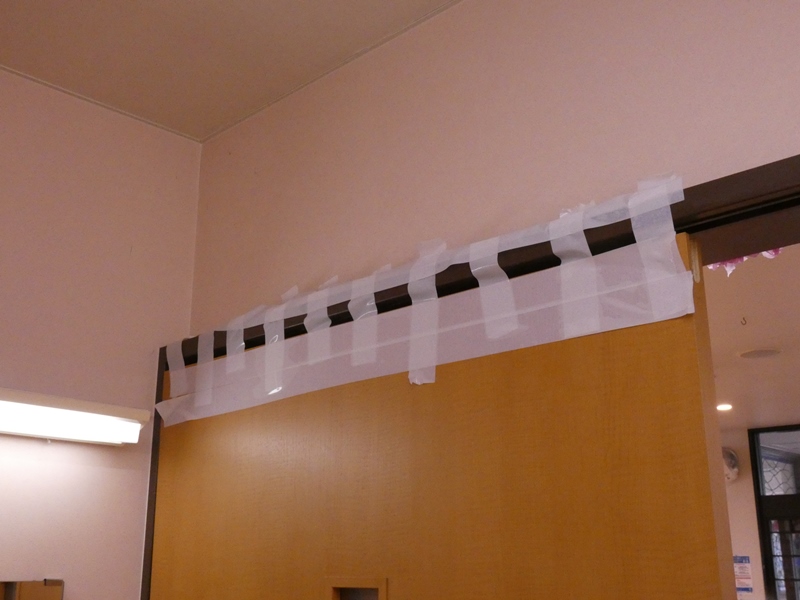
工房からそう遠くないデイケア施設からのご用命です。
男性用トイレエリアへの出入り口にスライドドアが取り
付けられています。車椅子での出入りもあるので幅が
広く重量もそれなりです。鴨居にレールが埋め込まれ、
その中を往復するローラー付き金具で吊り下げられた
構造です。摺動抵抗が小さく、楽に開け閉め可能です。
|
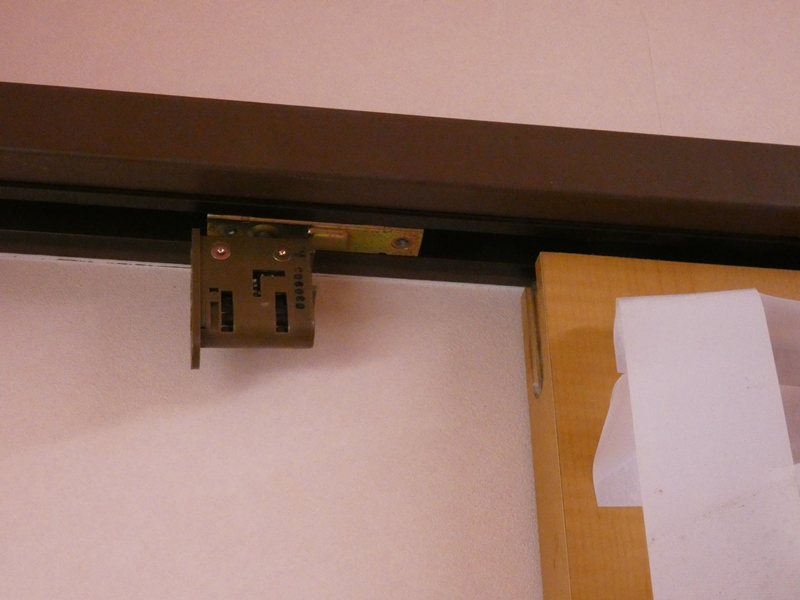
ドアパネルの上方両端に、このような
吊り金具が埋め込まれています。
|
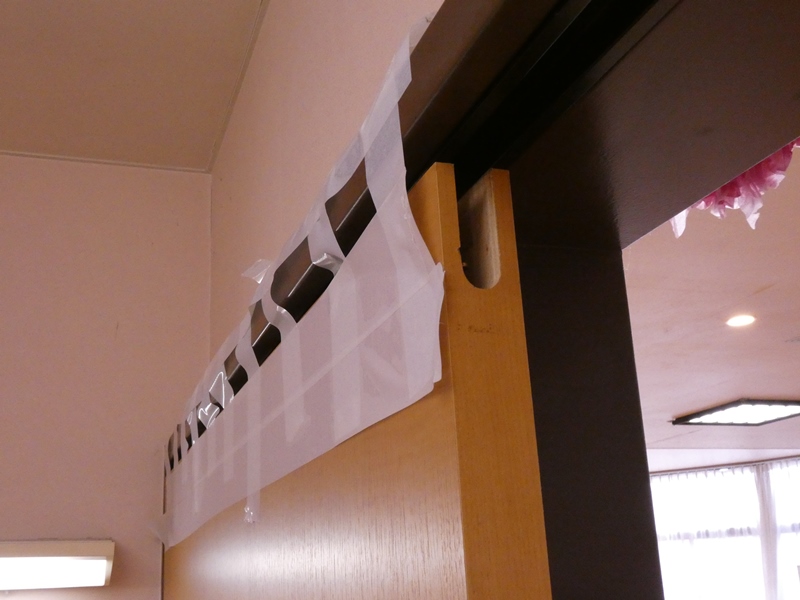
パネルの上方木端面に、金具を
埋め込む溝が正確に彫られています。
|
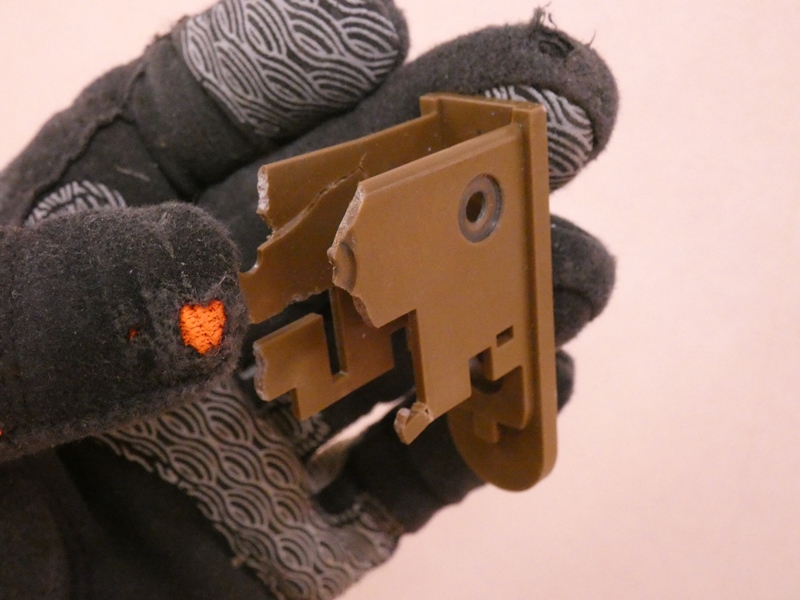
一方(手前側)の吊り金具がこの有様です。金属製部品を
内包しパネルと結合させるため、一体成型の樹脂製部品が
使われています。長年にわたり荷重に耐えてきた結果か、
あるいは何か無理な力が加わったのか、溝の中で大破して
います。実はこれまで同様の修理を何度か経験しており、
いずれも新しい補修部品に交換することで解決しています。
|
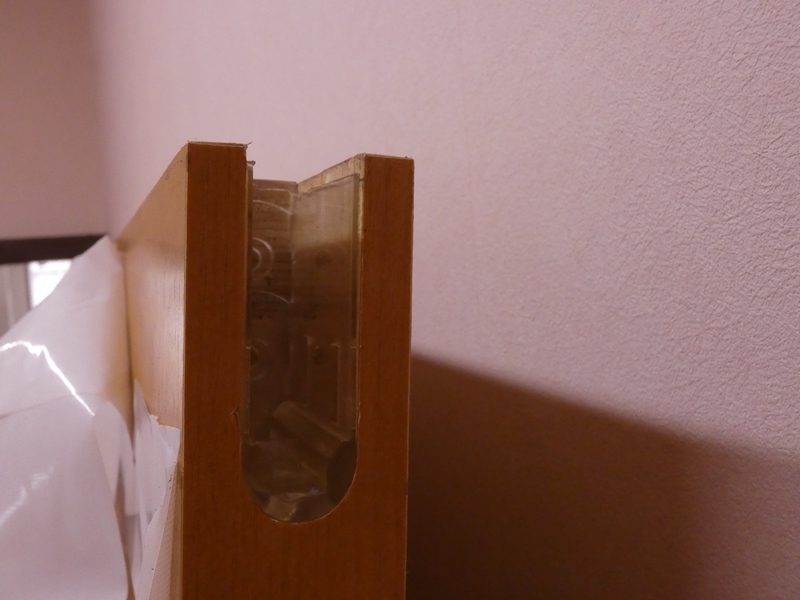
溝の中にはもう一つ別の樹脂製
部品が取り付けられています。
|
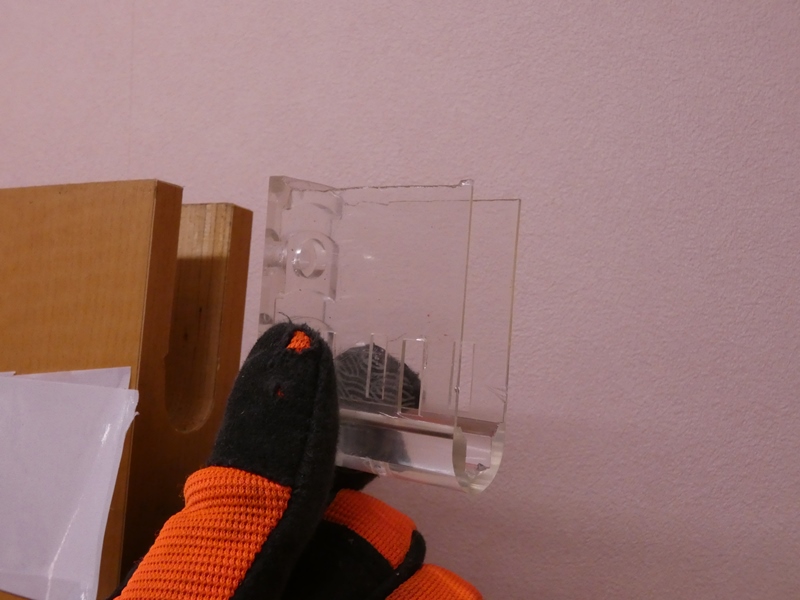
2つの樹脂製部品はアウター(この部品)とインナーの
関係にあり、アウターは予め溝内にネジ固定されます。
|
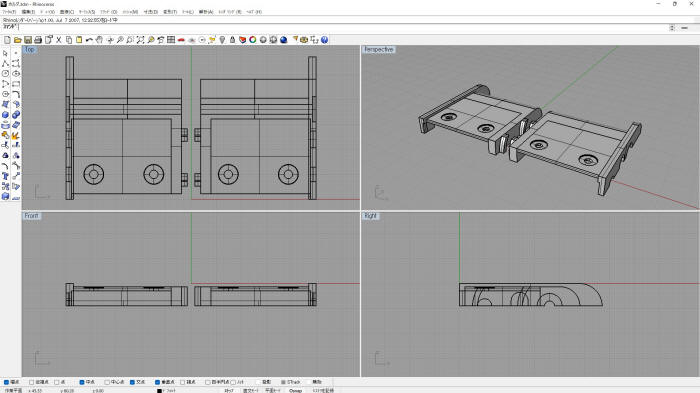
以前と同様に補修部品を探すべくかなり時間を費やすのですが、
今回はサイズがひと回り大きく、堅牢なローラーが使われていて、
流用できそうな製品が見つかりません。知り合いの住宅設備屋
さんに聞いても見たことがないそうです。もちろん型番もメーカーも
全く記載がありません。かくなる上は、作り出すしかありません。
|
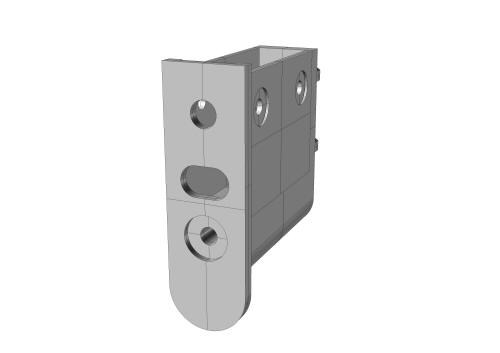
壊れていないパネル後方の吊り金具を取り外し、ノギスで
精密に採寸して元の形状を割り出します。CADに取り込み
さえすれば、3Dプリンターで造形が可能になります。原形は
割と壁に厚みのない箱状をしています。このままではFDM
方式の3Dプリンターでは出力しづらく、内部の金属製部品の
組み込みも面倒になりそうです。ひと工夫が必要です。
|
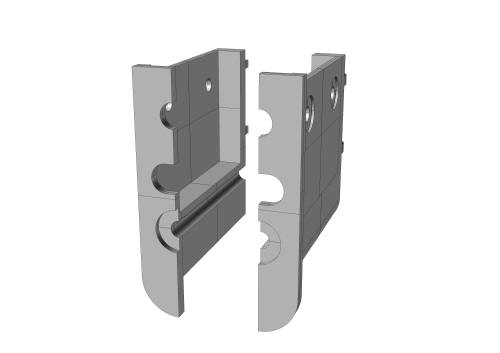
ボックス形状を左右に2分割することにします。金属製
部品を挟み込む構造にすれば、組み立てが簡単です。
3Dプリンターが使用するPLAフィラメントは、樹脂用の
接着剤により非常に強力に接合が可能です。加えて、
吊り金具全体がパネルの溝内でアウターの内部に
納まるので、強度的には心配ないと思われます。
|
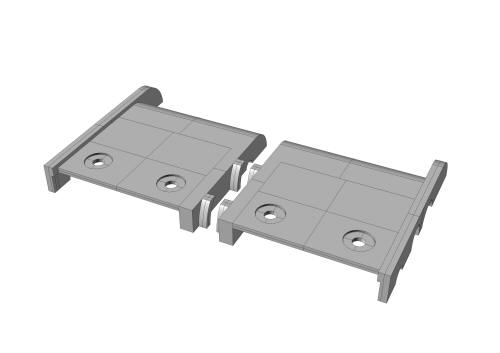
2分割した各部を水平方向に並べます。この状態で
標準の3DフォーマットであるSTL形式にてファイル
出力します。色々検討しましたが、3Dプリント時に
どうしてもサポートの付加が避けられません。
|
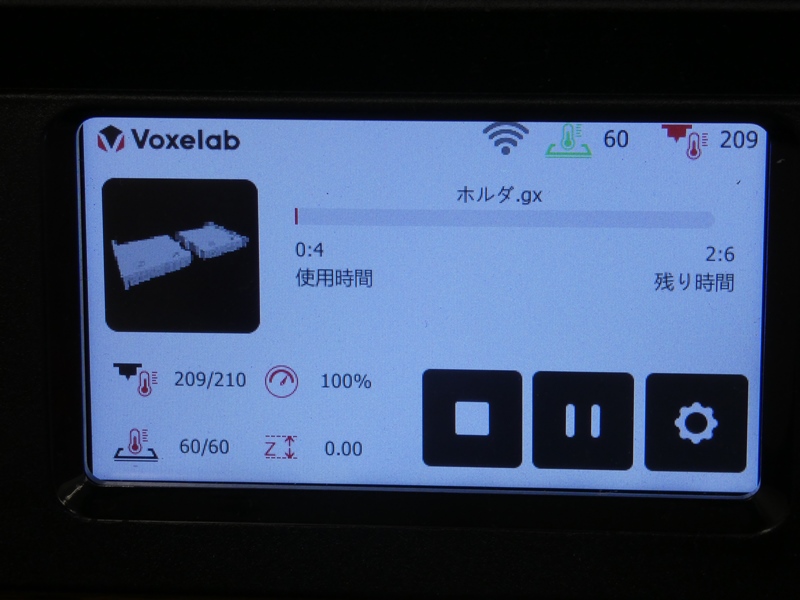
スライサーによる処理を経て工房の
Voxelab
Ariesにデータを送ります。
|
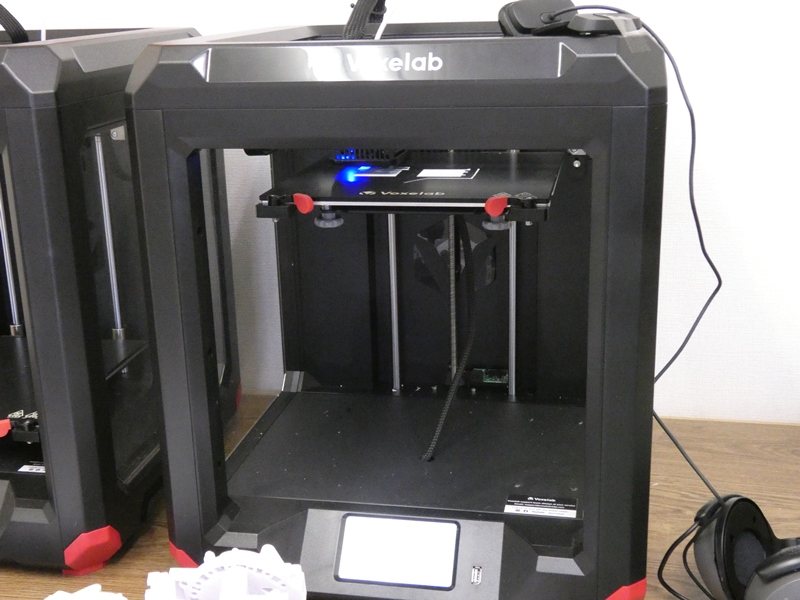
ベッドおよびホットエンドの加熱が
完了し、出力が始まります。
|
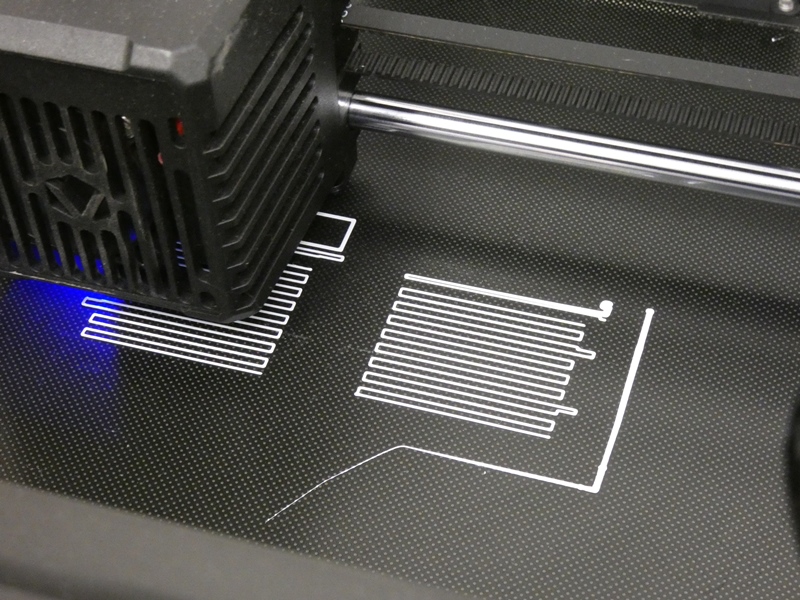
これまで安定して出力されているので安心し
切っていますが。1層目をプリントしています。
|
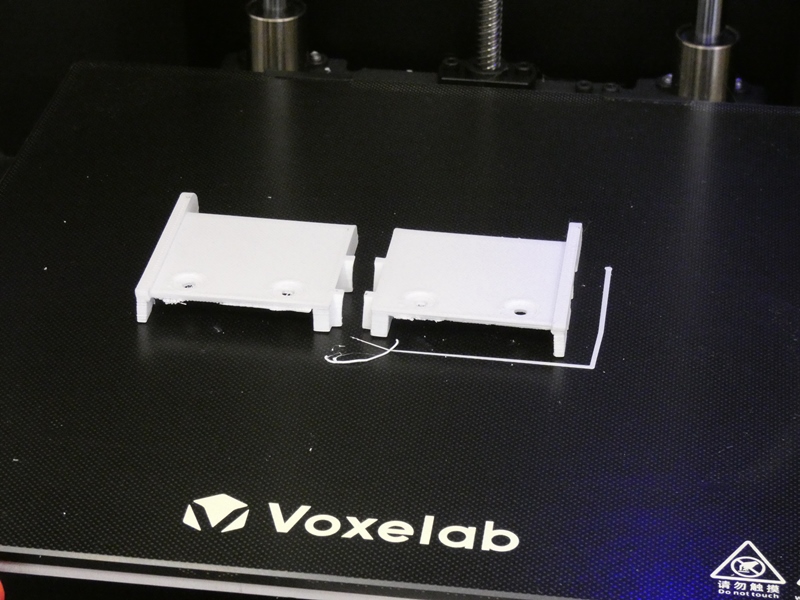
強度を考慮し充填率は100%です。
2時間ほどでプリントが完了します。
|
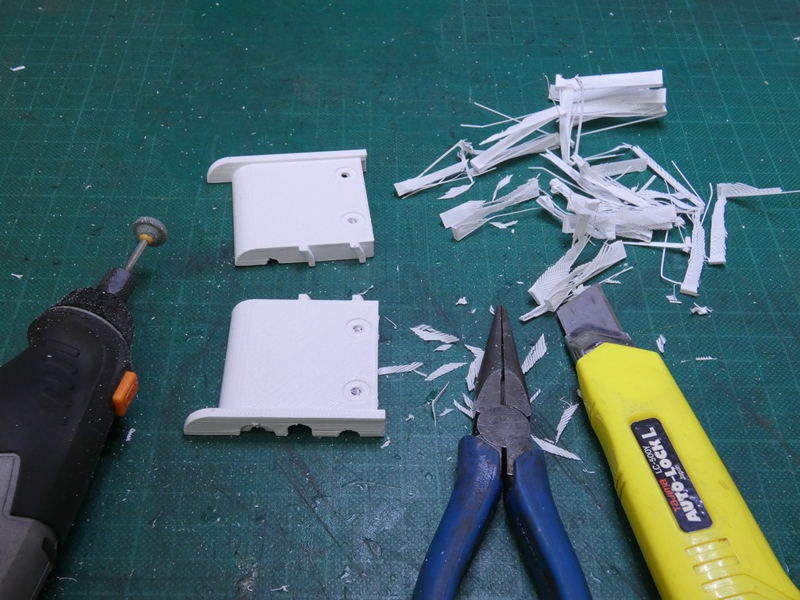
内側の中空部分に成形されたサポートを取り
除きます。Ariesのスライサーは今ひとつです。
|
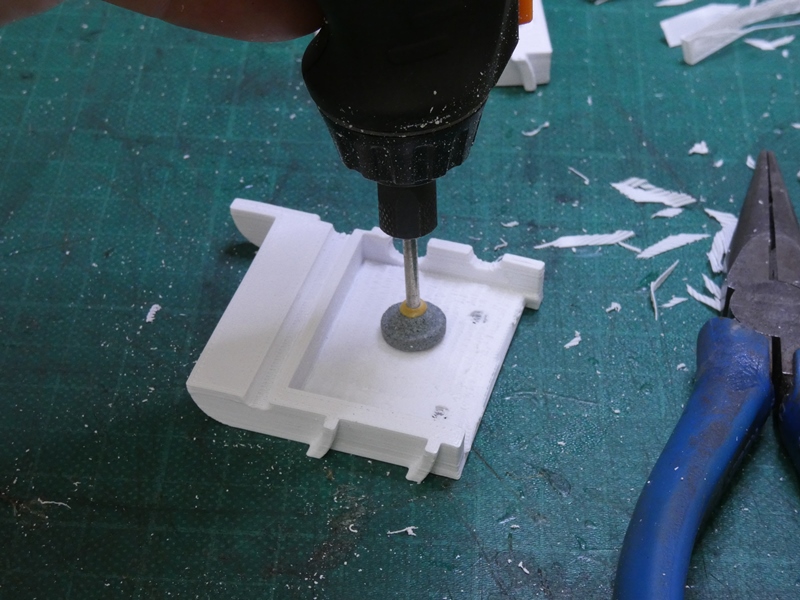
サポートを取り去った痕がかなり乱れて
います。ルーターを使って表面を整えます。
|
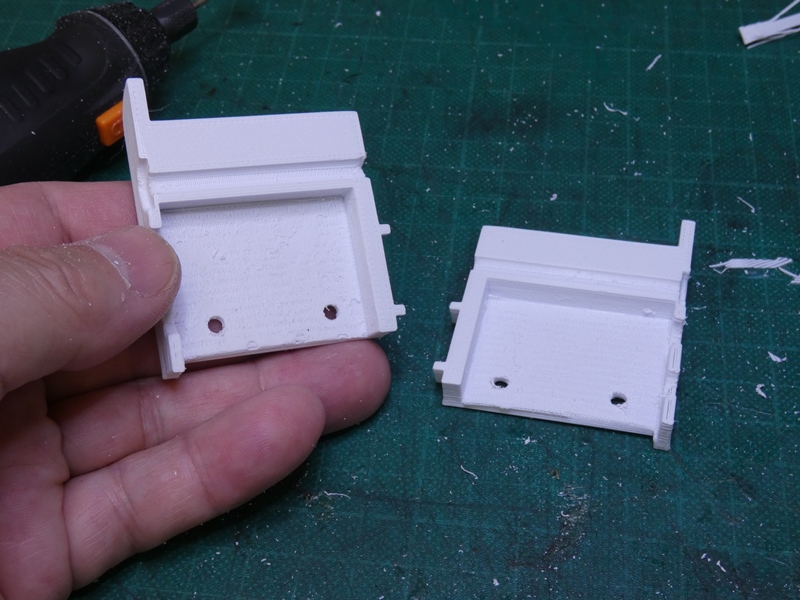
3Dプリンターなら部品が一発で出来上がると思い
きや、なかなかそうは行かず手直しが必要です。
|

分割した2個の部品を合わせてみます。
設計通りに成形されているようです。
|
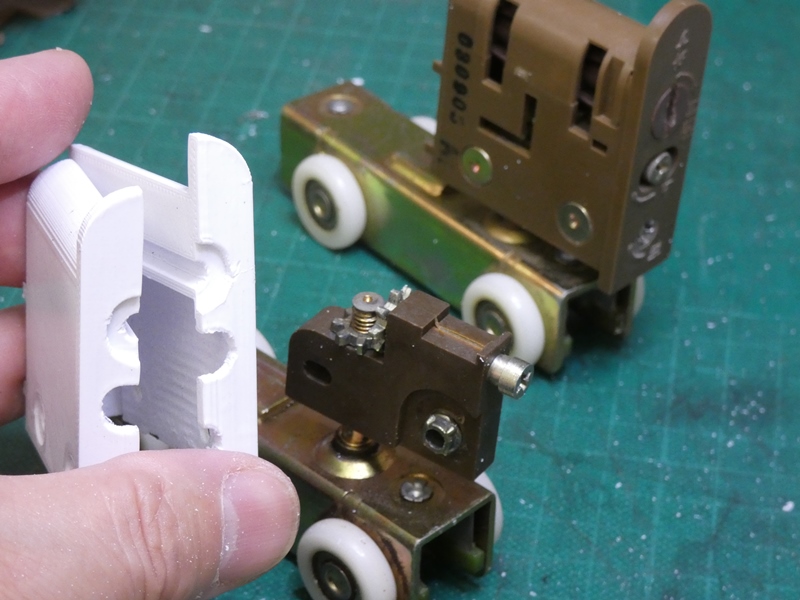
金属製部品と組み合わせてみます。
写真奥は壊れていない元の状態です。
|
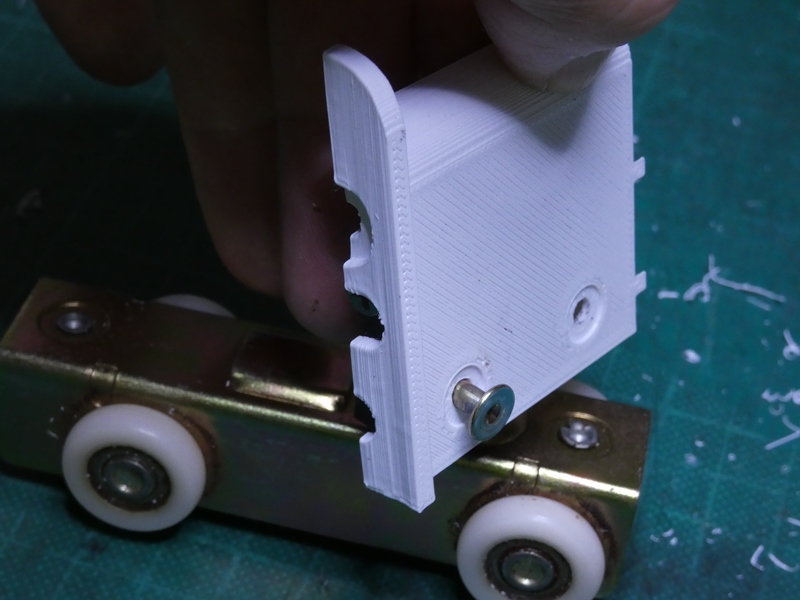
両者を結合するピンを通します。ピン
2本にパネル重量の半分がかかります。
|
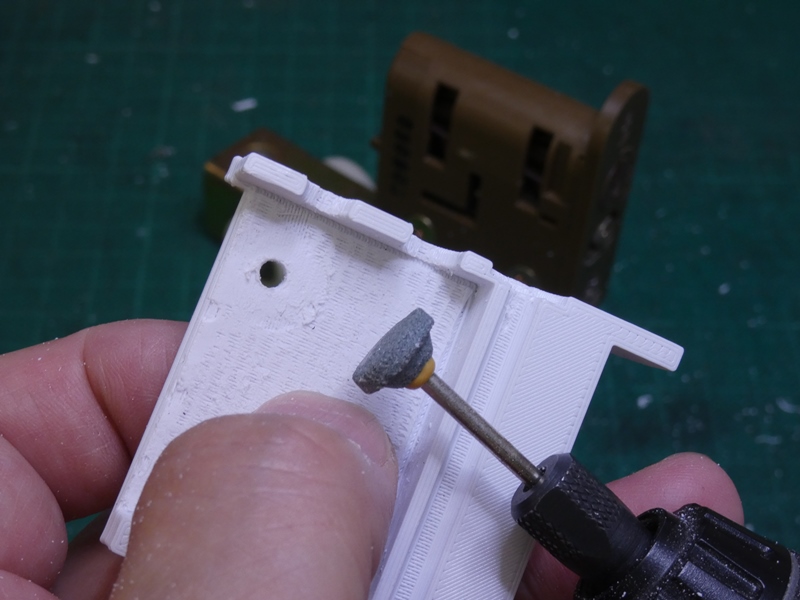
内側に干渉があるようなので調整します。
大きな荷重が加わるので最小限にします。
|
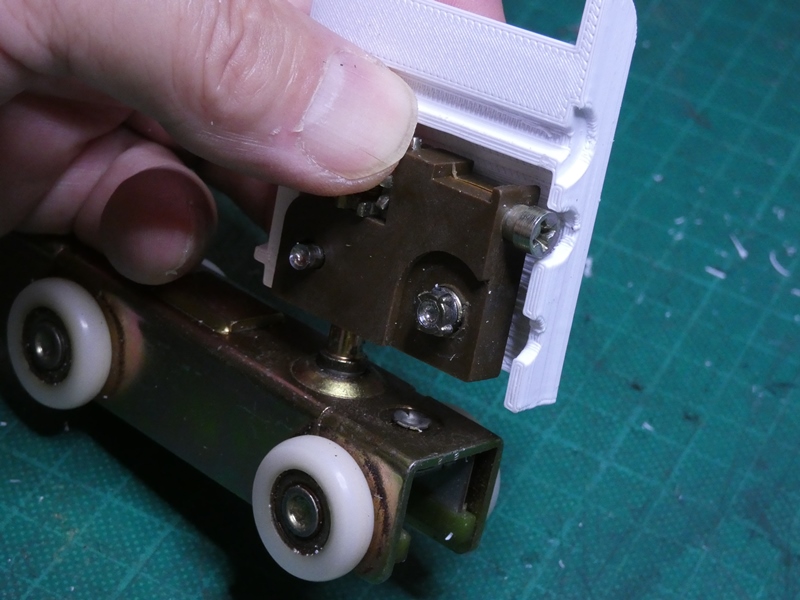
2本のピンを介して樹脂製部品に荷重が伝達され、
前後2枚の薄い壁面がパネルの重量を支えます。
|
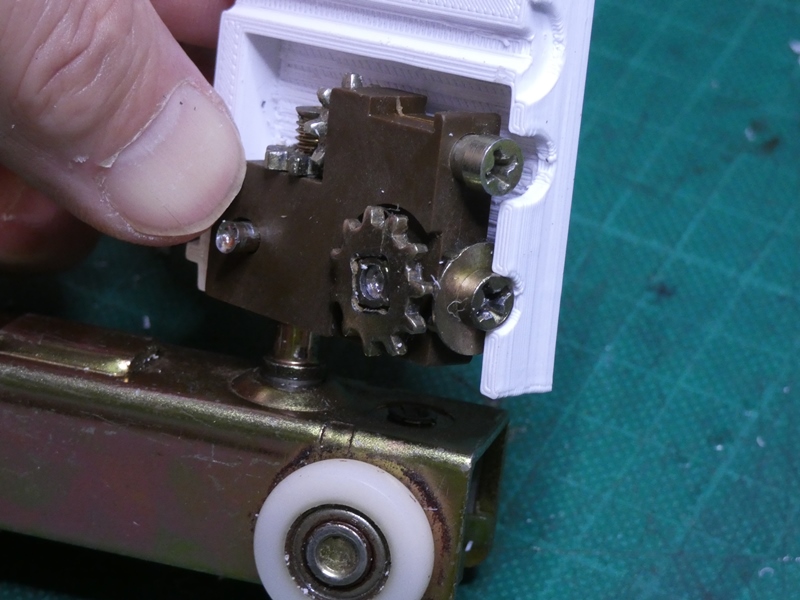
パネルの水平位置を調整する、
歯車の付いたネジを組み込みます。
|
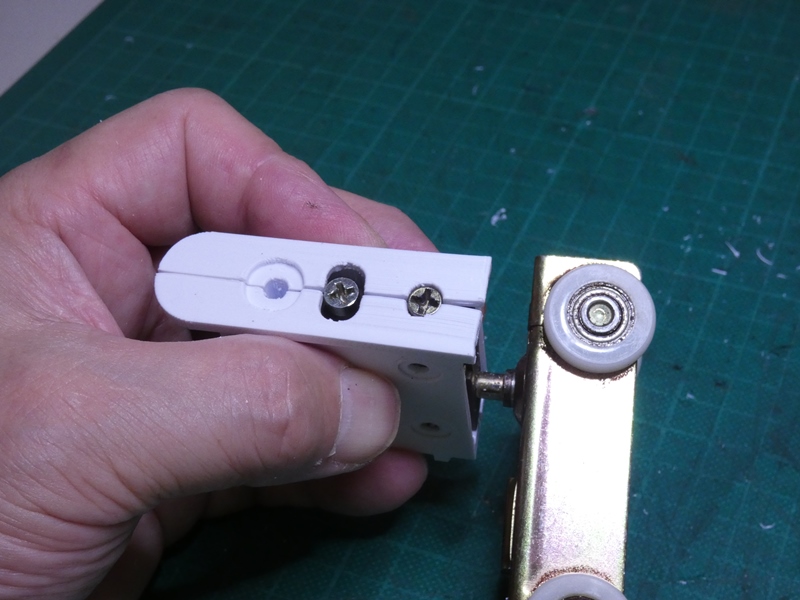
やはり2枚が密着しません。プリント中にベッド
から部品が剥離し、成形が歪んだためです。
|
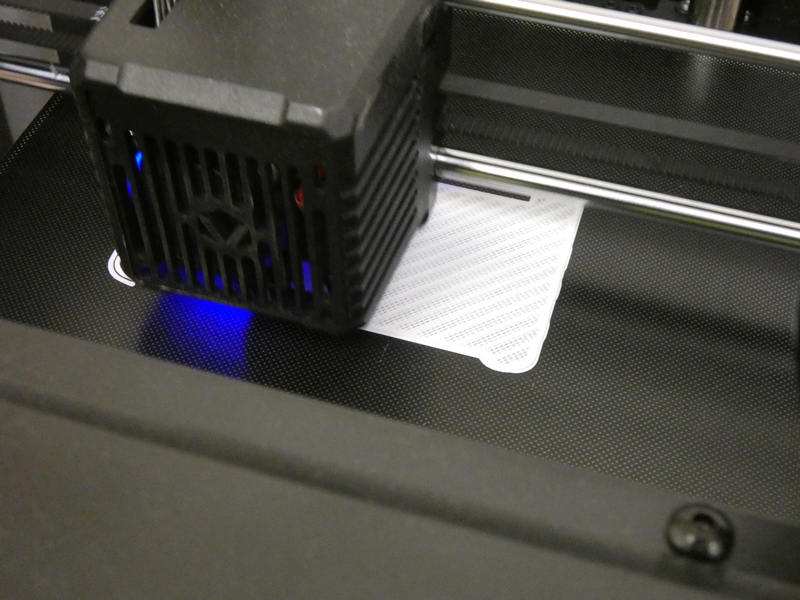
歪み(反り)を極力小さくするため、プリント
開始時にラフトを付加して出力し直します。
|
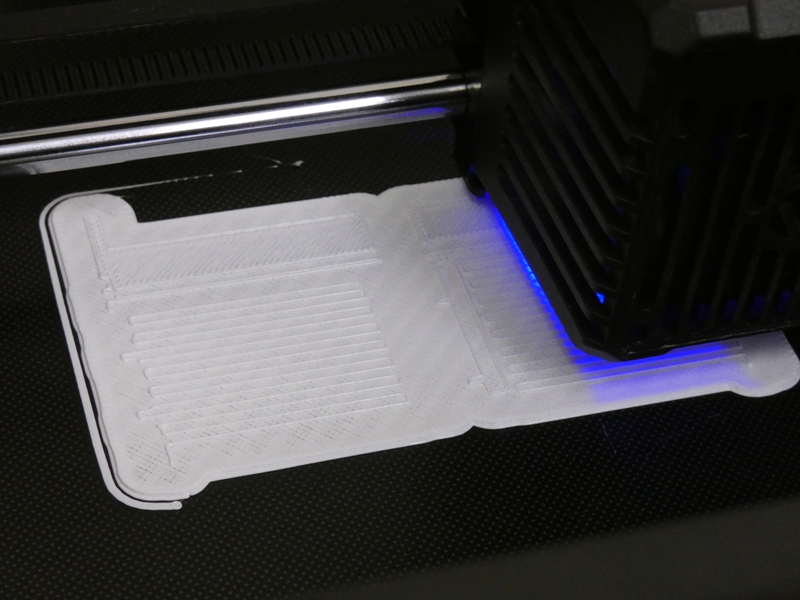
満足のいくまで何度でもトライできるところが、
デスクトップマニュファクチュアリングの強みです。
|
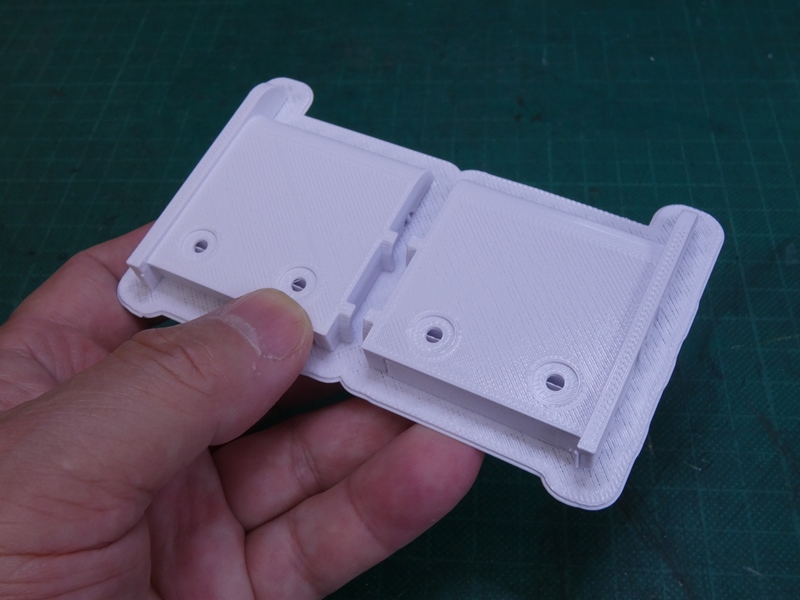
ラフトが付加された状態で出力が完了しました。Ariesに付属する
スライサー(Voxel Maker)は、特に設定を変更せずとも良好な
出力をもたらしますが、ことサポートとラフトに関しては、剥がし
にくく綺麗に除去できない、にもかかわらずベッドへの固定も
今ひとつ・・と手放しで喜べるものではありません。Slic3Rや
CURAなど他のスライサーを検討するべきかも知れません。
|
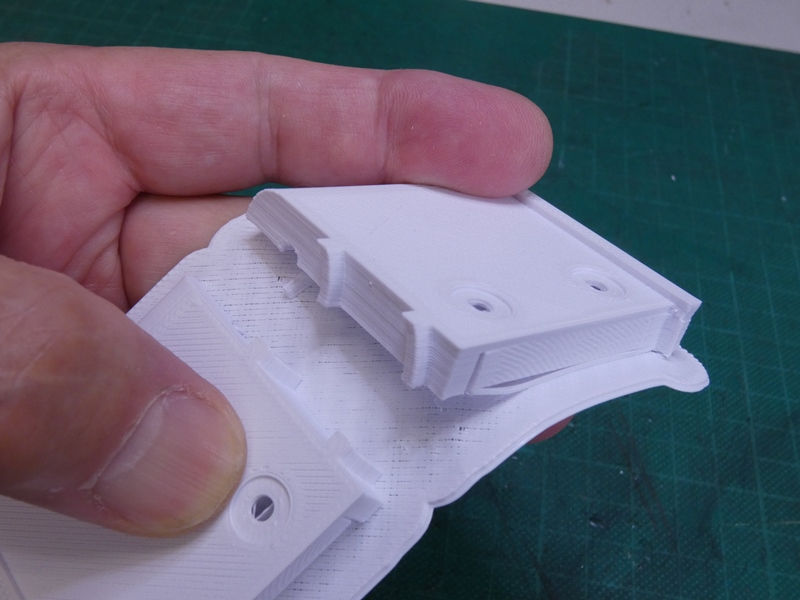
本体とラフトが結構強く付いています。
引き剥がすのにやや力が必要です。
|
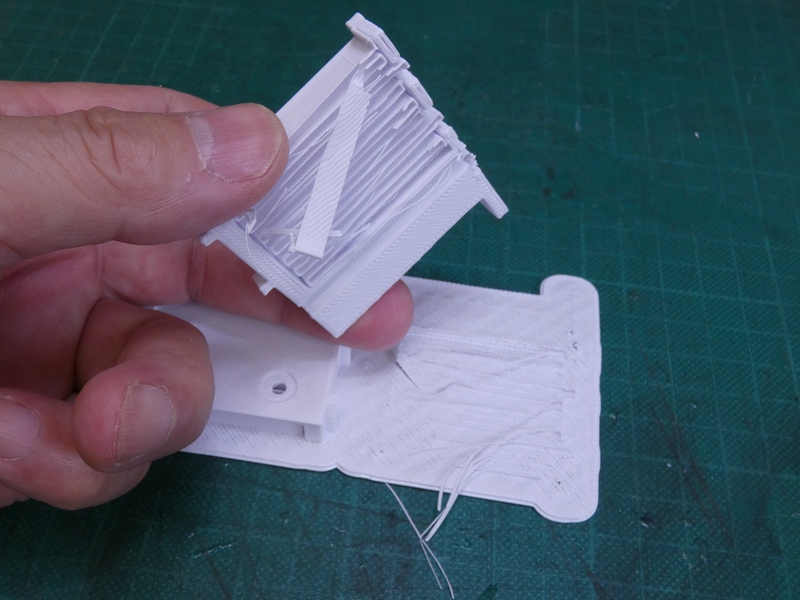
ラフトを分離すると、またこのサポートです。
パラパラ勝手に外れてくれると楽なのですが。
|
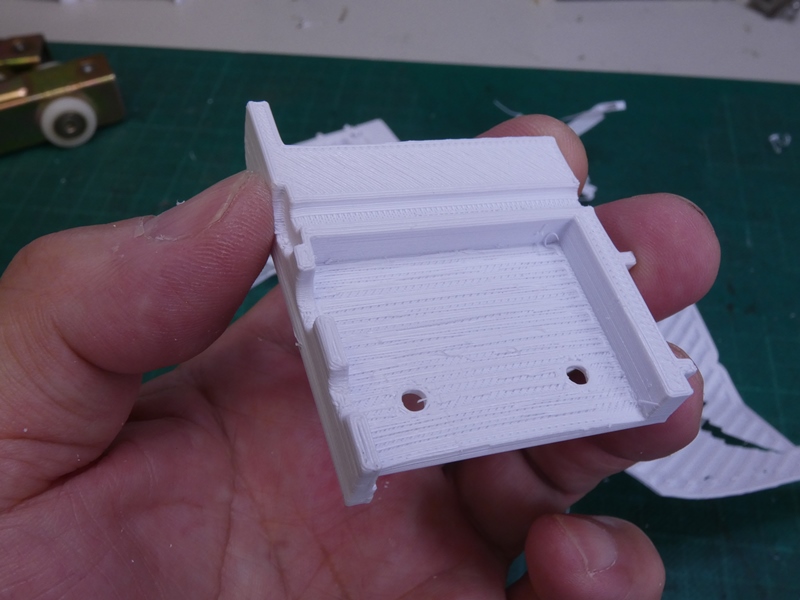
最悪なのはサポートを取り除いた面(上面の
裏側)が、このようにひどく荒れることです。
|
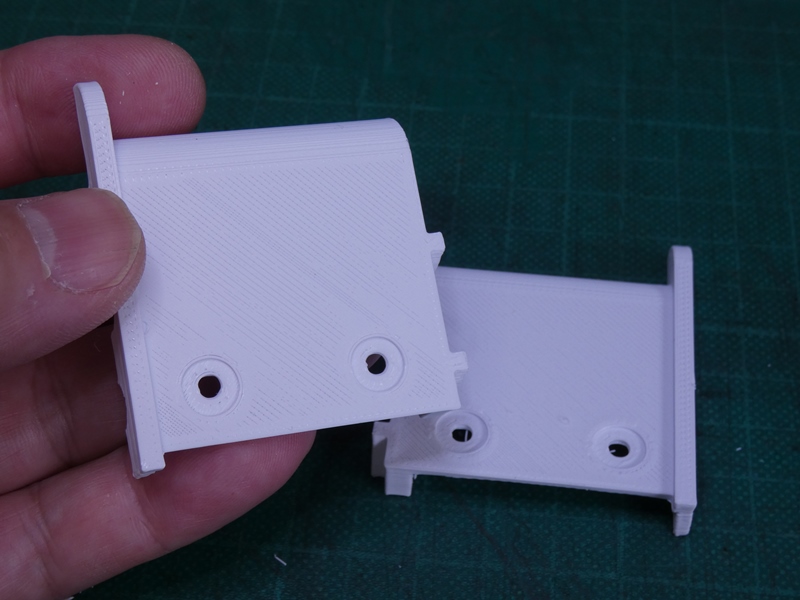
かなりの手作業を経て、何とか
実使用できる状態まで仕上げます。
|
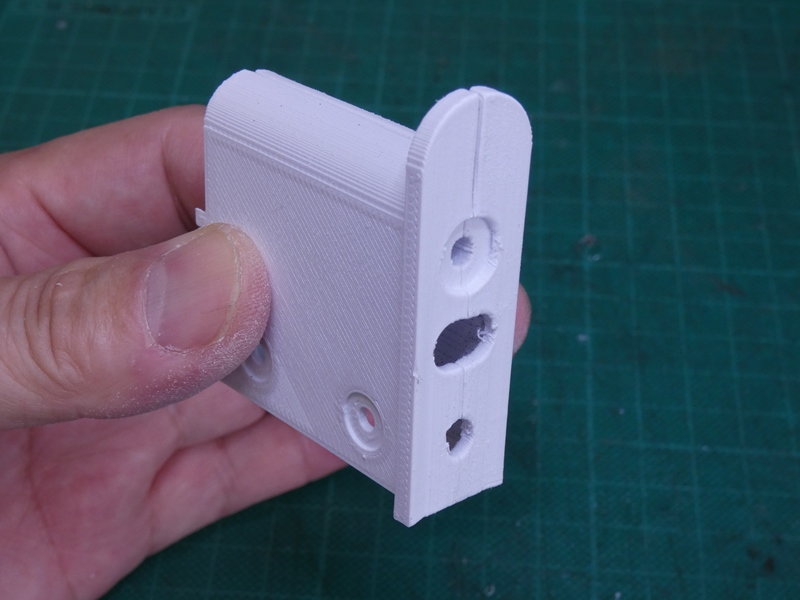
2個の成型部品のみを合体させてみます。ほとんど歪み(反り)も
なく、正確に組み立てられそうです。プリントし直す際に、内側での
干渉を回避するようデータを若干修正しました。CADのメリットです。
|
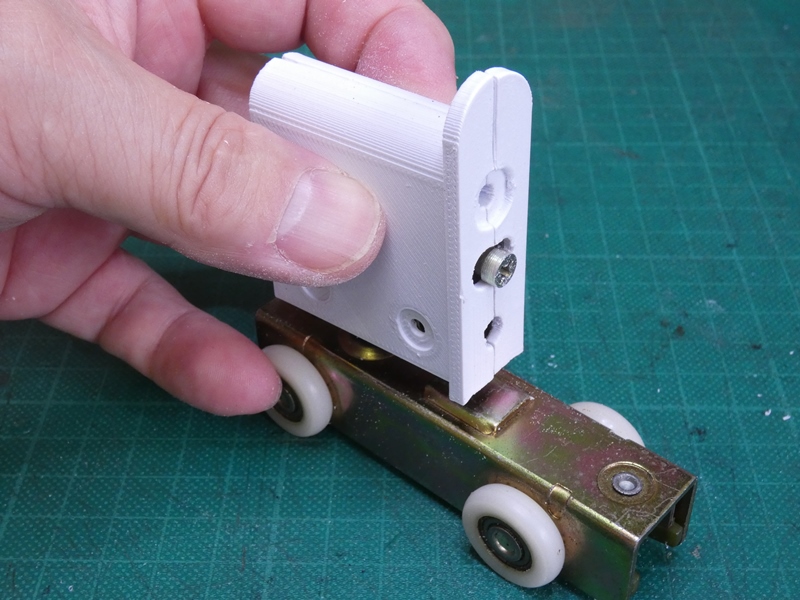
金属製部品と合わせてみます。
干渉もなく正確に合体します。
|
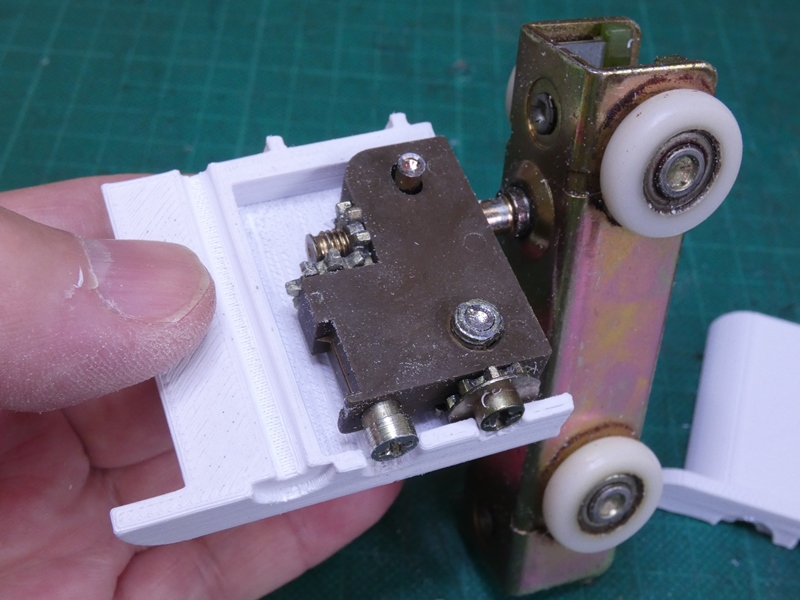
歯車付きネジと2本のピンをセットし、
組み立てる位置を正確に合わせます。
|
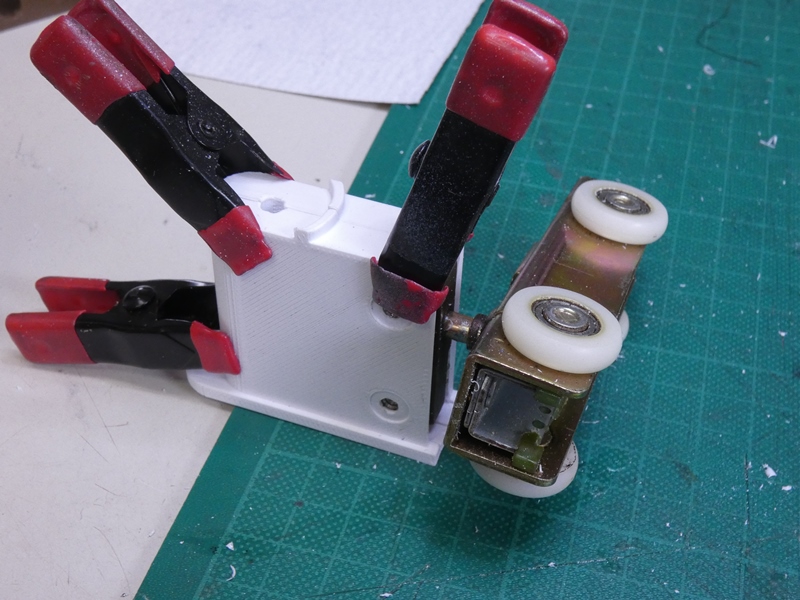
周囲を数個のクリップで挟み、仮固定します。
合体位置にズレがないか再度確認します。
|
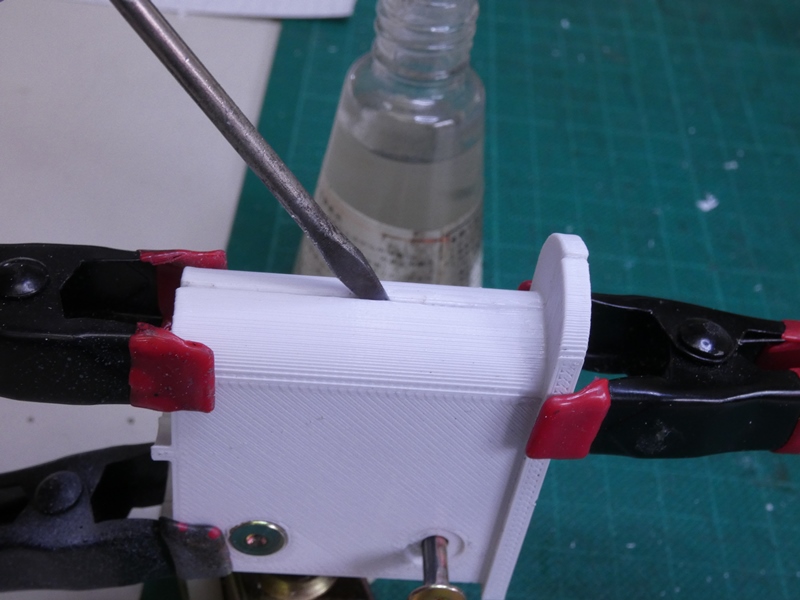
この状態で接合面に接着剤を流し込みます。
様子を見ながら全周にわたり接着します。
|
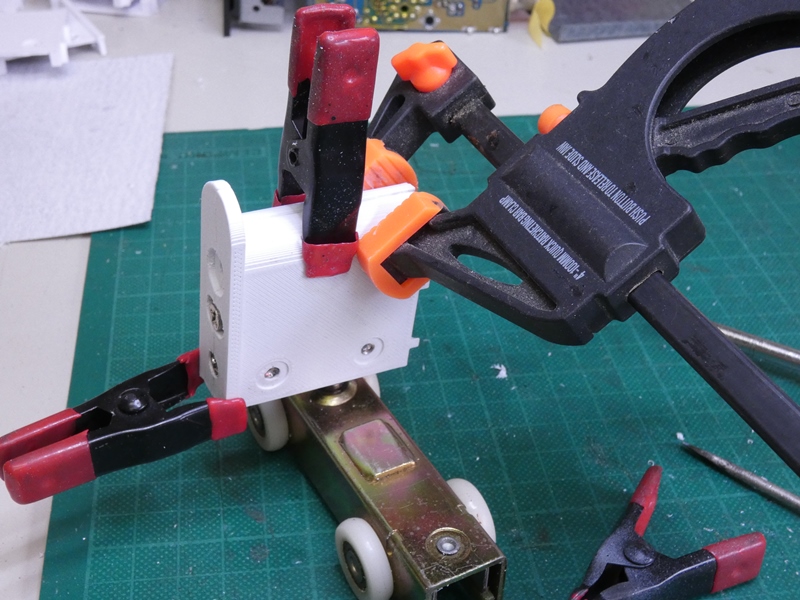
接着剤はアクリル用の二塩化メチレン溶剤です。溶剤により
母材が溶け出して混ざり合い、間もなく溶剤が蒸発することで
材料が一体化し強固に接合します。接着材ではなく材料自体
の強度に接着力が依存します。完全に固化するまで待ちます。
|
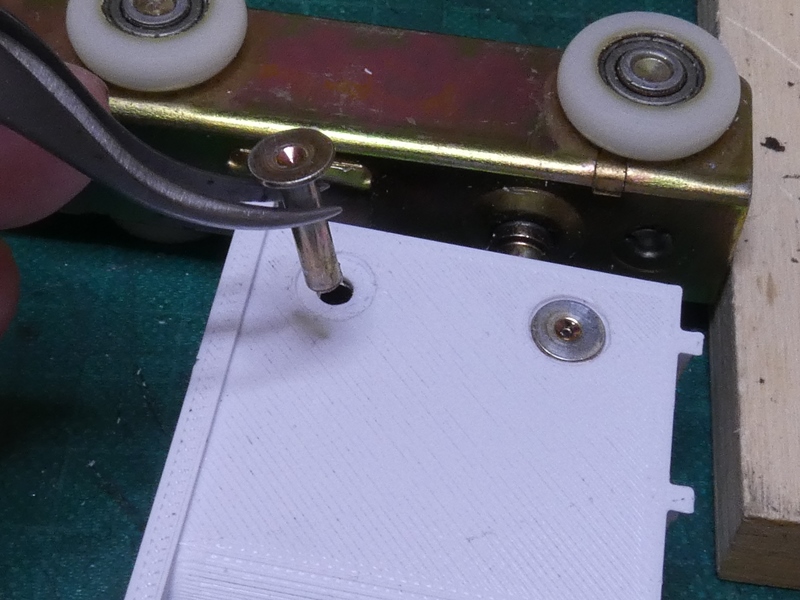
樹脂製部品と金属製部品を結合するピンは、片側に
ワッシャを通してカシメることで固定されていました。
|

分解する際にカシメを壊してしまったので、
別の固定方法を考えなければなりません。
|
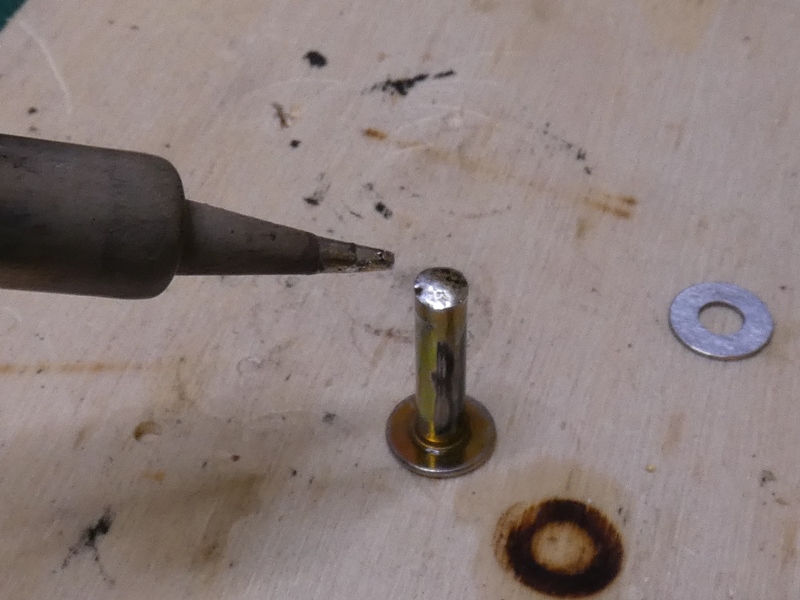
まず、ピンの先端部分に、後で半田付けしや
すいよう、フラックスを付けて半田を盛ります。
|
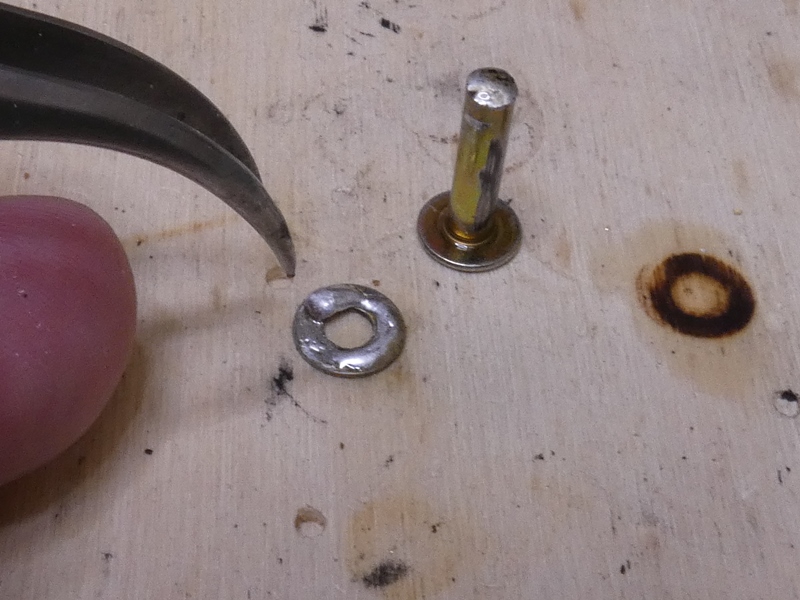
ピンに通すワッシャにも、その
周囲に半田を盛り付けておきます。
|
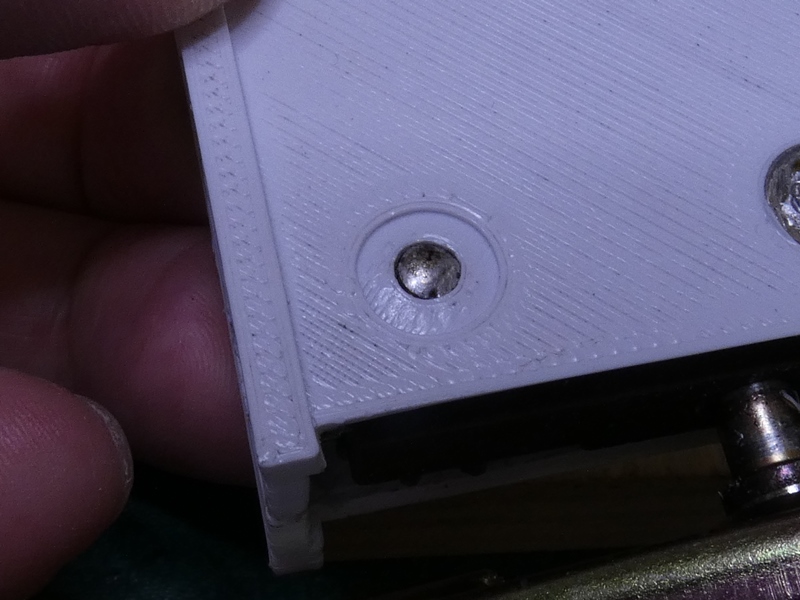
200度程度で溶融するPLAなので、
半田付けに耐えられるわけがありません。
|
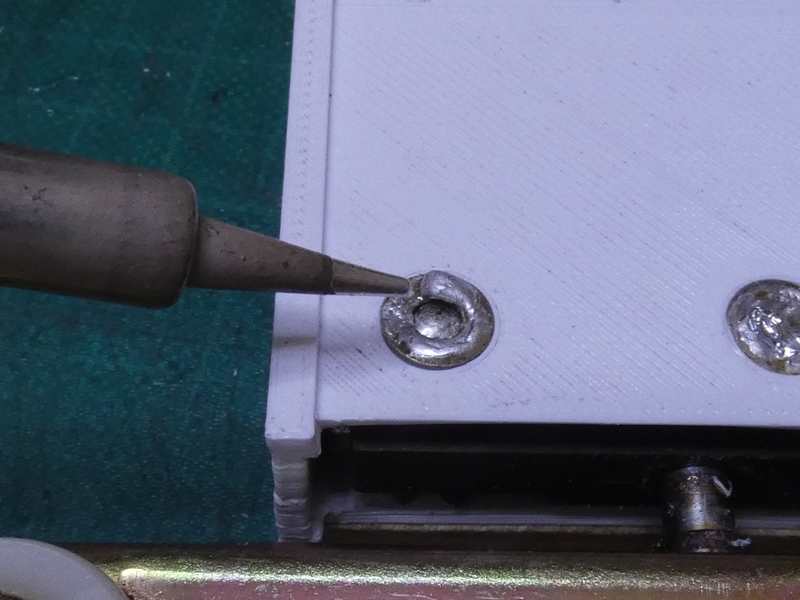
ですが、予めピンとワッシャに半田を盛り付けておけば、
瞬間的にこて先を当てるだけで半田がつながります。
|
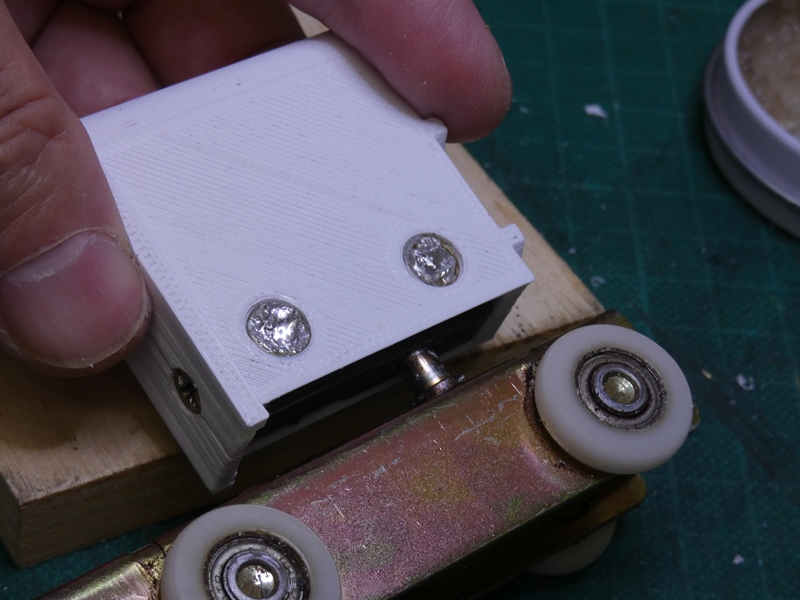
先ほどのアウター内に収まれば、ピンが抜けてくることはないのですが。
それにしても、ピンの位置からローラーのある方向には、数ミリの壁面が
残されているだけです。ここにドアパネルの重量が集中するわけですから
強度的に問題がないのか心配です。ただ、元の部品がこの通りの設計
なので、現状に倣うまでです。万一壊れたら・・、再度作り直すまでです。
|
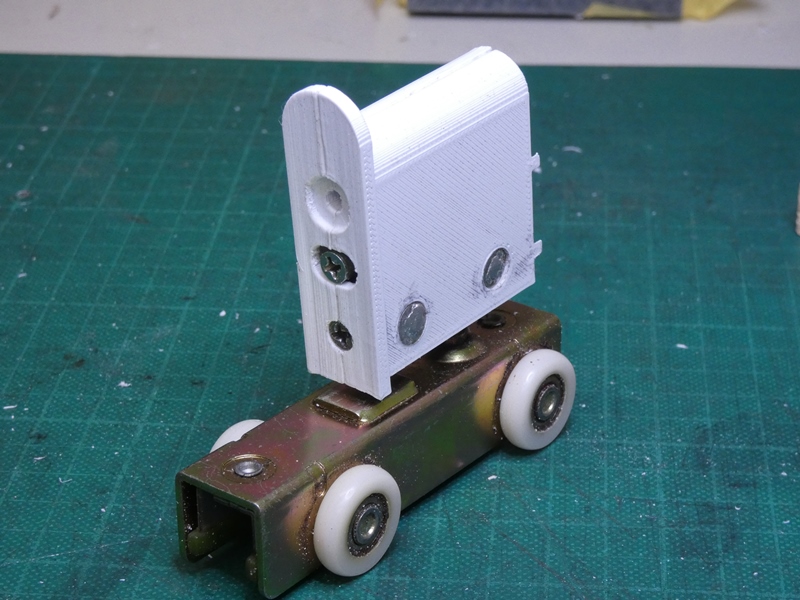
本体の接着も完全に固化し、完全に破壊
してしまった吊り金具が、晴れて蘇りました。
|
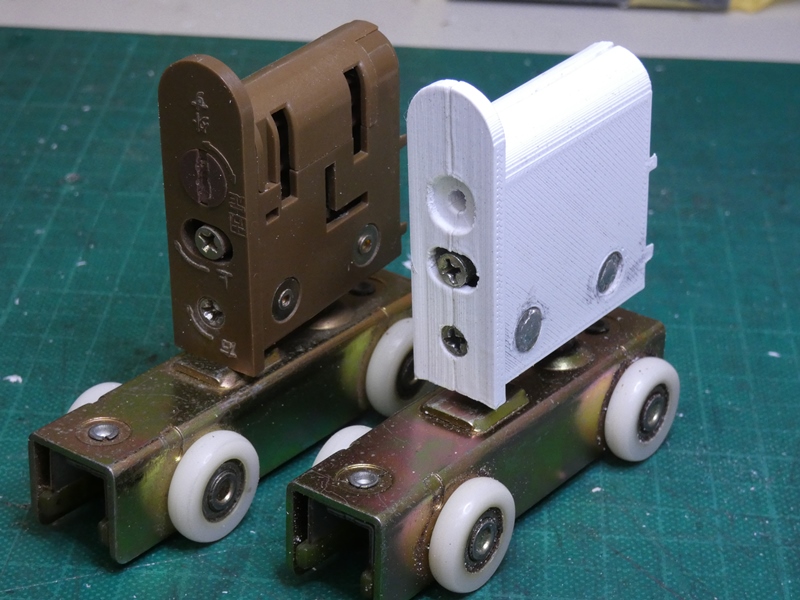
アウターと結合させる回転ツメを略したので、同位置に
長いコーススレッドを打ち込んでパネルに固定します。
|
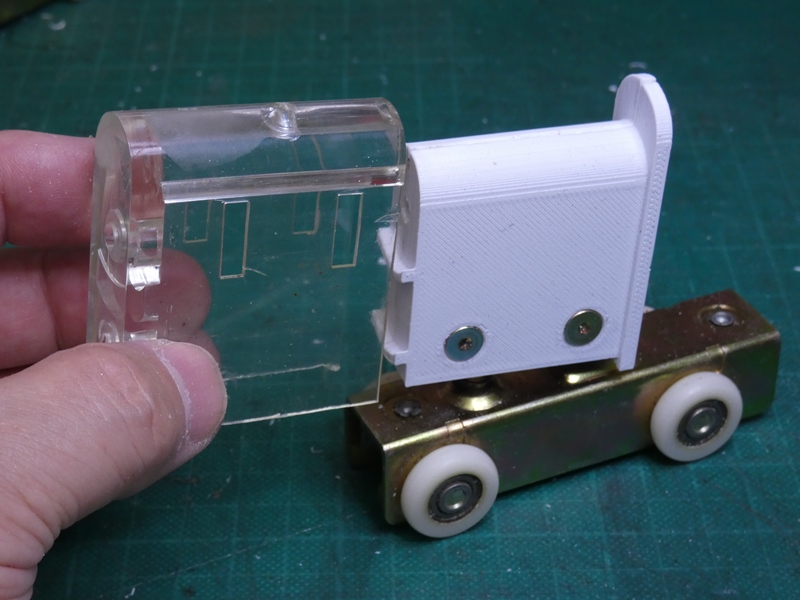
アウターを被せてみます。アウターの奥突き
当り面に弓型の溝が刻まれていますが、
|
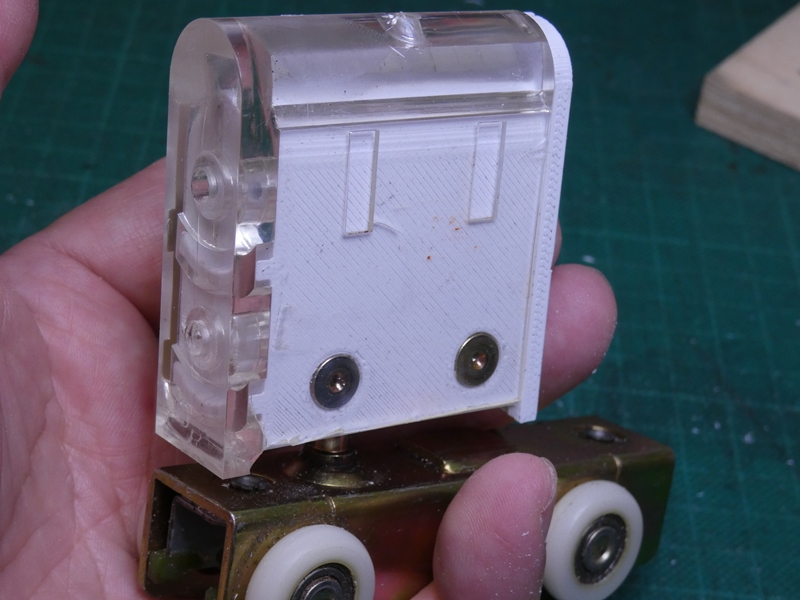
プリントした部品の側面に同じく弓型の
突起があり、溝に入り込む構造です。
|
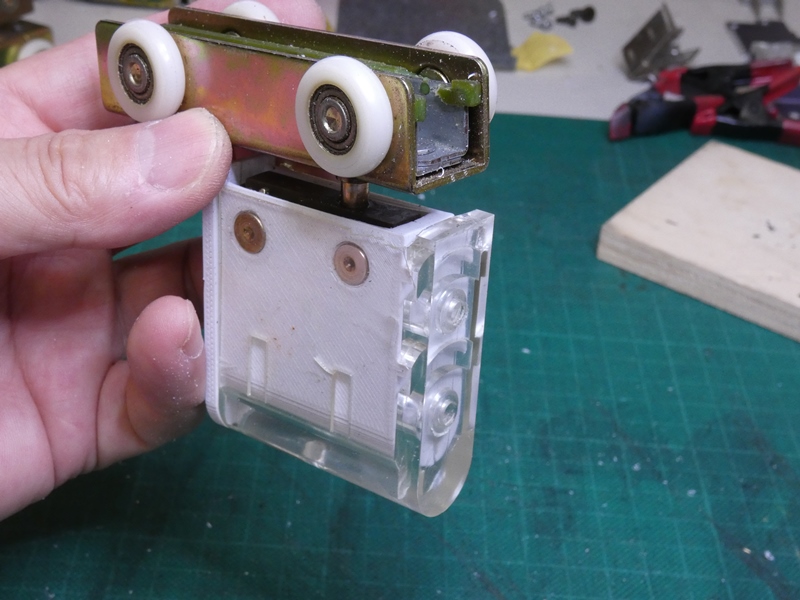
突起が溝に嵌まることでパネルの荷重はアウターに伝わり、
アウターはドアパネルの溝内でネジ固定され、さらに貫通
するコーススレッドにも支えられてドアを吊り下げるわけです。
|
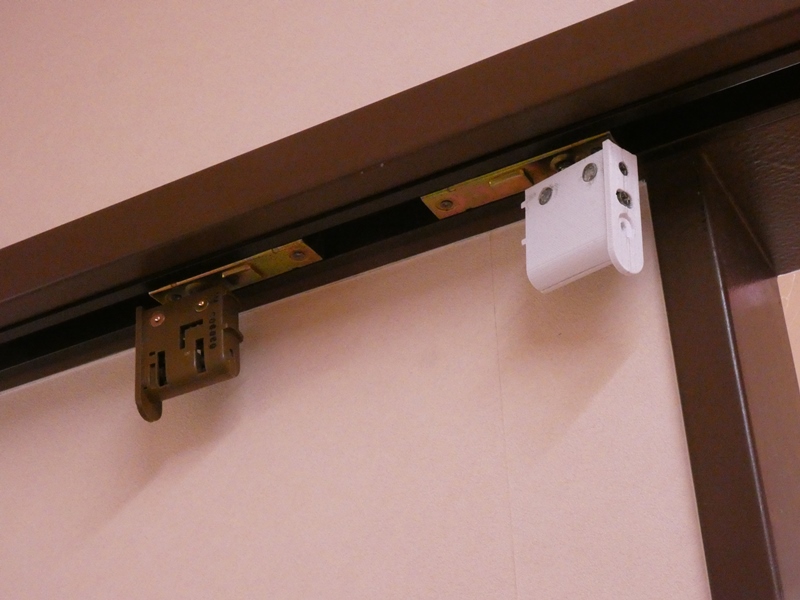
再生した吊り金具を携えて現場に戻ります。実は吊り金具を
レールに入れるには、鴨居からレールを外す必要があります。
|
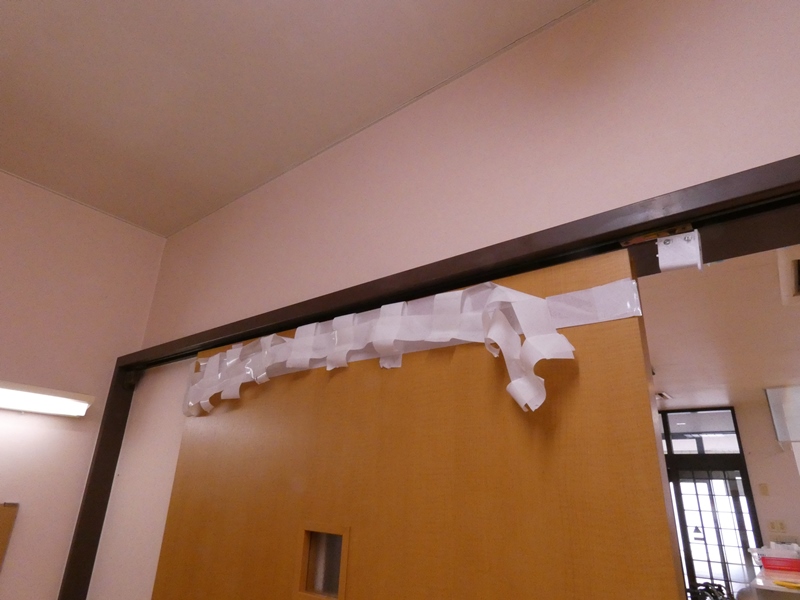
間隔を空けた吊り金具の間に
ドアパネルをセットします。
|
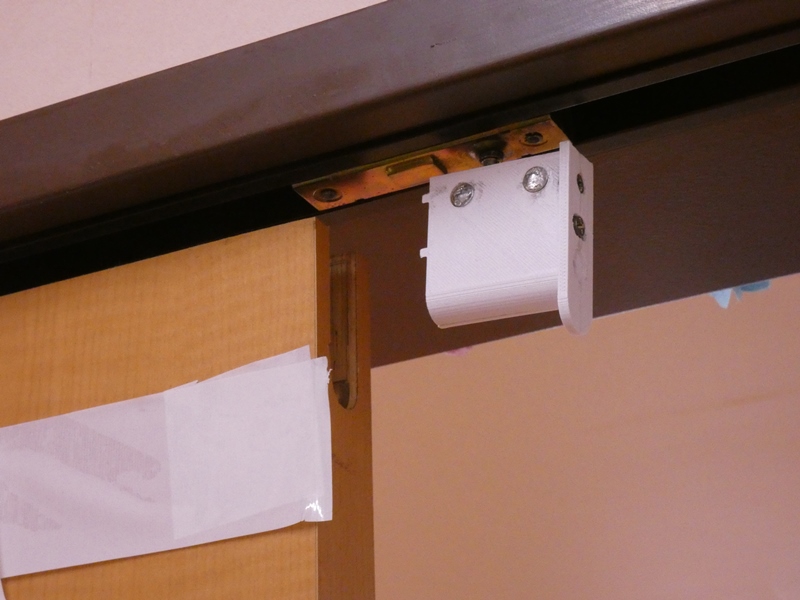
力を込めてパネルを持ち上げ、位置を合わせて吊り金具を
差し込みます(その前にアウターを固定しておきます)。
|
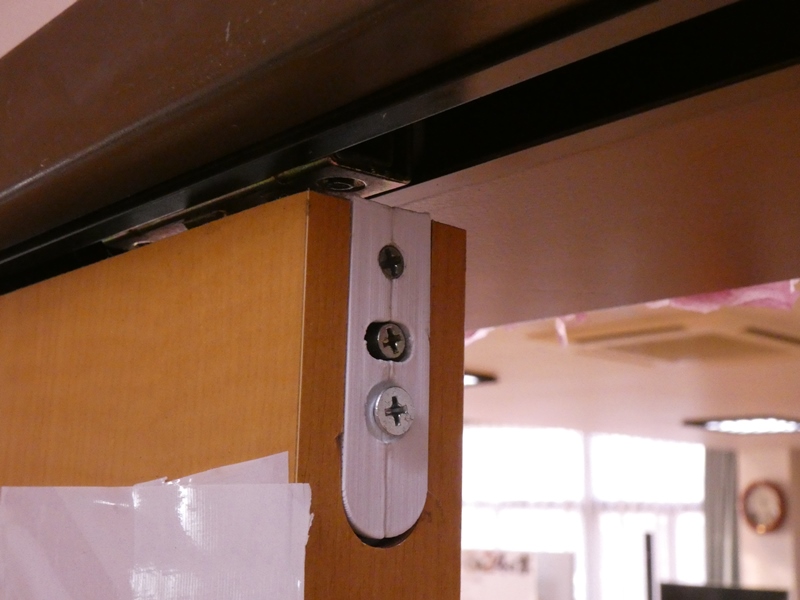
アウターとの結合用に使われるはずの穴に、吊り
金具を貫通する長さのコーススレッドを打ちます。
|
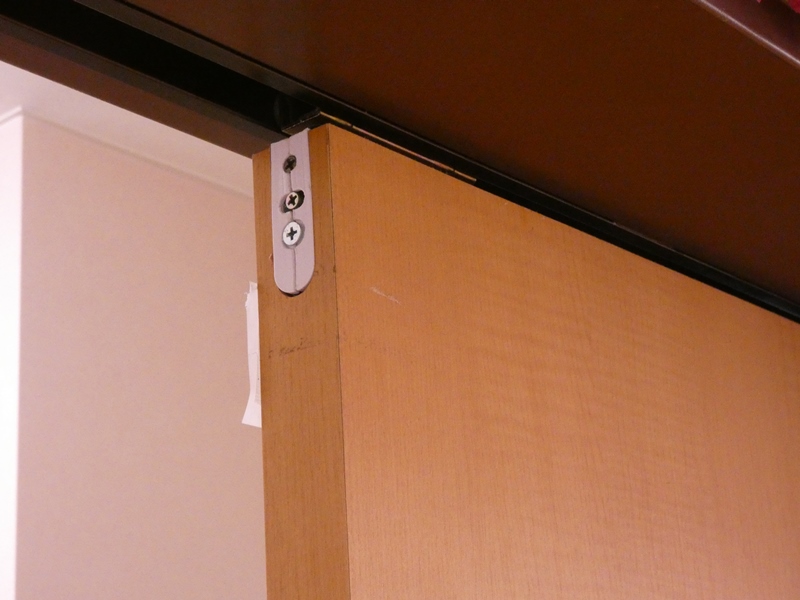
何とか・・なりました。プリントした樹脂製部品が壊れやしないか
ビクビクです。最初の開け閉めはゆっくり静かに動かします。
|
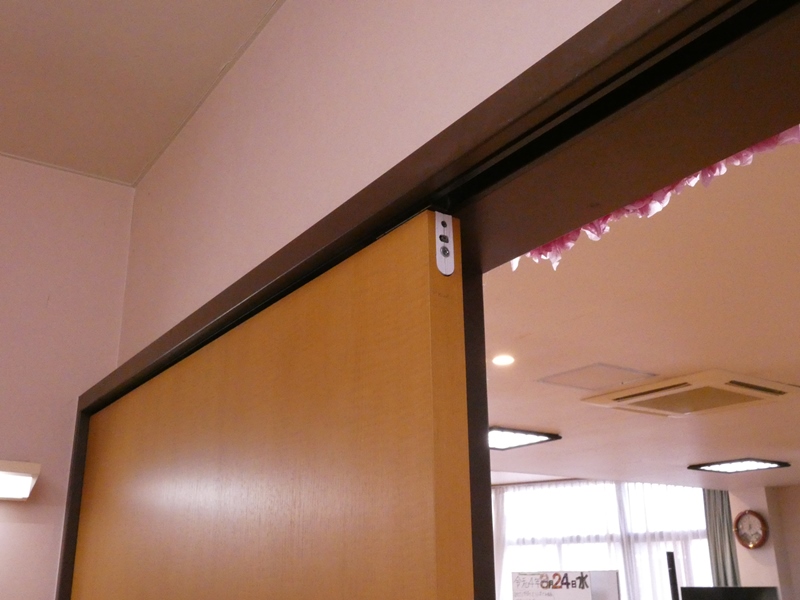
定位置で吊り下げられていれば、
開閉はスムーズなものです。
|
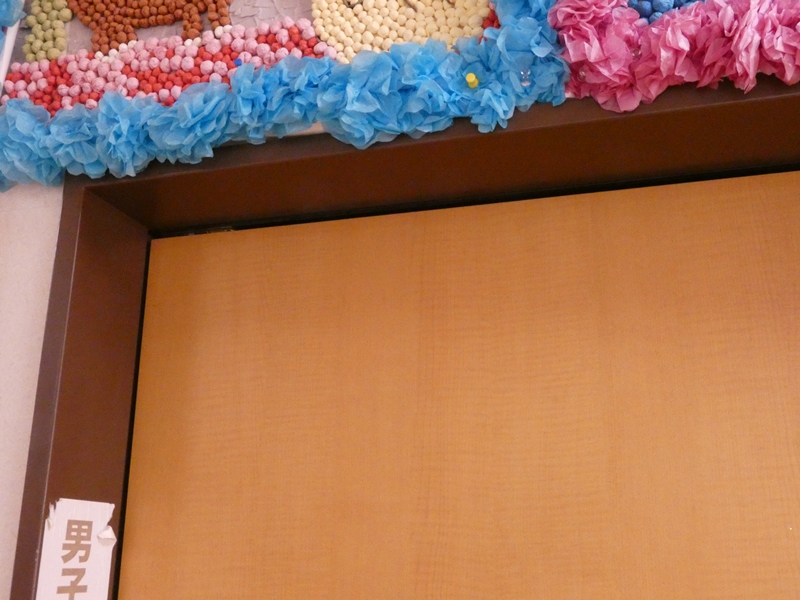
施工後1週間ほど過ぎた頃に恐る恐る様子をお聞きしてみると、
「極めて良好!」との嬉しいお返事をいただきました。数日のうちに
樹脂部分が破断しドアパネルが再び落下する事態を心配しており
ましたが、それなりの強度が保たれているようです。ドア開閉時に
かかる進行方向の力や衝撃は、ローラーが転がることで十分に
低減され、吊り金具にはほとんど及びません。しかも開閉の両端で
ダンパーが作動するので、衝撃もごく小さなものでしかありません。
逆にドアパネルに正面から衝突するような場合が心配です。ドアの
下端には長さ方向に溝が彫られていて、1か所だけ床から突き出た
ピンで支えられているだけです。ドアパネルが捻れる方向に力が
加わると、さすがに吊り金具は無事ではいられないでしょう。元の
部品もこの衝撃が繰り返されて破損に至ったのかも知れません。
|
|
|